Efficient livestock operations depend on durable flooring. Regular inspections of concrete slats and support beams are crucial for preventing costly replacements and maximizing the lifespan of your facility. Industry best practices recommend checking slats and beams after each cleaning cycle, with annual inspections for breeding and gestation facilities. This proactive approach helps identify developing issues before they necessitate immediate replacement.
When it comes to replacement, particular attention should be given to supporting beam integrity, as beam deterioration can lead to significant structural failures. Regular inspections should include examining both sides of support beams using a flashlight through slat openings. Look for developing cracks, particularly in areas above columns, as these can allow moisture penetration, leading to internal structural damage.
Key inspection points include:
- Surface wear patterns around feeders and waterers
- Cracks in individual slats
- Beam condition, especially near support points
- Bearing surface adequacy (At least 3” of bearing surface should be present on a column or end wall pocket)
- Signs of uneven slat positioning
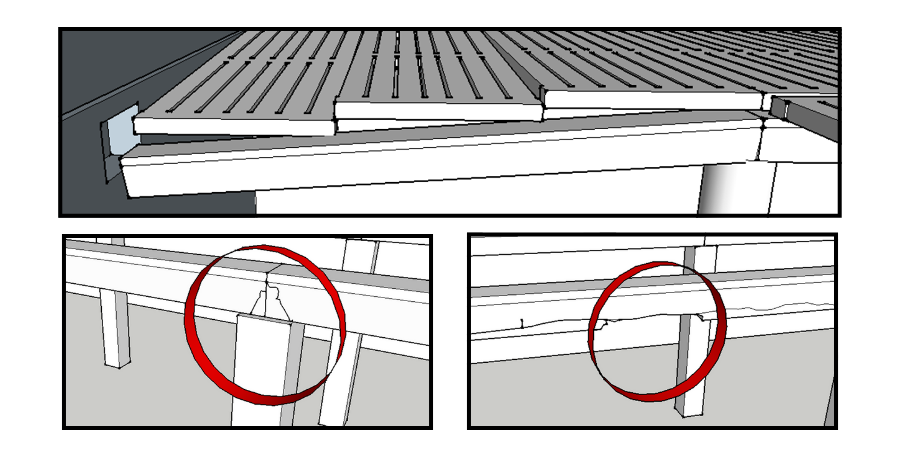
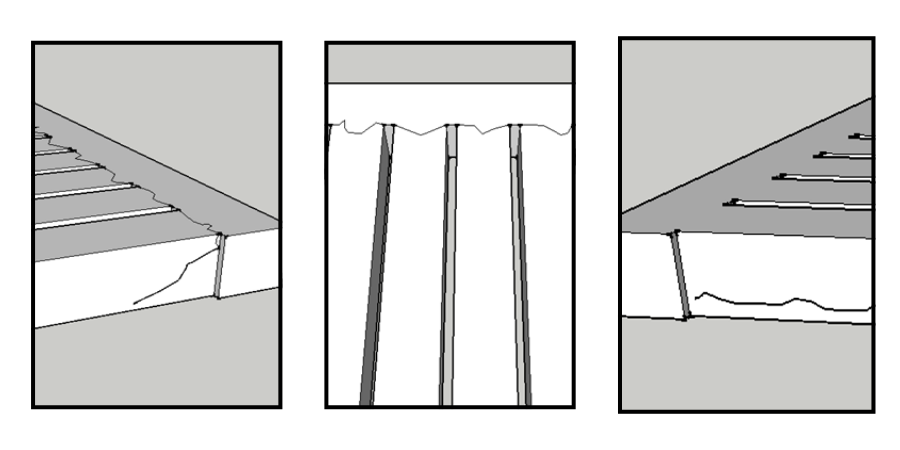
Photo example of individual slat cracks to look for when evaluating slat condition.
The financial implications of proper maintenance become apparent when considering complete replacement costs. Industry data suggests that once 40% of slats show physical damage, complete replacement becomes more cost-effective than individual replacements, as the labor costs for replacing a large percentage of slats can equal the total replacement cost.
Maintaining concrete slatted flooring requires attention to detail and regular inspections. Prompt action when concerning issues helps ensure optimal facility performance and longevity.
To schedule your slat inspection, contact Chad Grouwinkel at 515-368-2730. The Hog Slat Field Guide provides practical, step-by-step instructions and valuable insights into effectively maintaining your concrete slatted flooring to extend its lifespan and ensure the well-being of your livestock. Prioritize your flooring maintenance—protect your investment.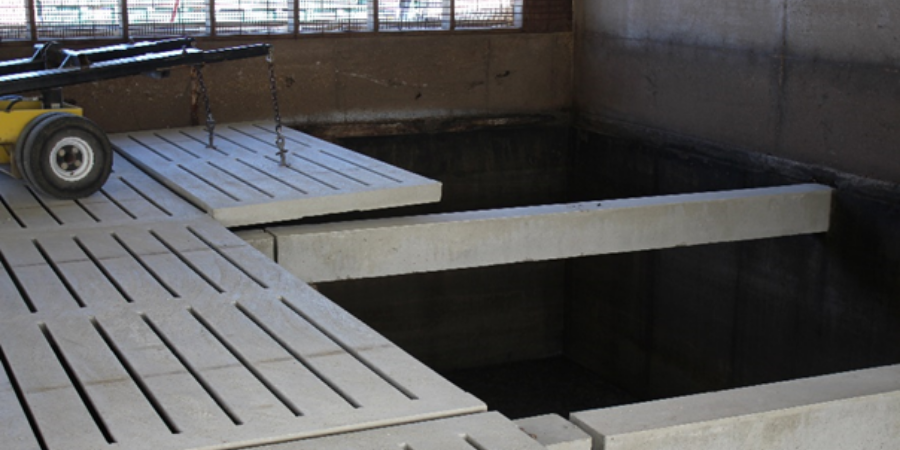