One of the benefits we list for the Grow-Disk system is a “superior chain.” The feed chain with molded plastic disks is the main component of the system, physically moving feed to a feeder or sow drop.
I dropped in on Hog Slat’s engineering group to see what I could find out. I found Tim Hawkins, the project engineer for the Grow-Disk product line. Tim led me to a complicated looking run of 12 corners occurring in less than eight feet with intersecting vertical and horizontal corners.
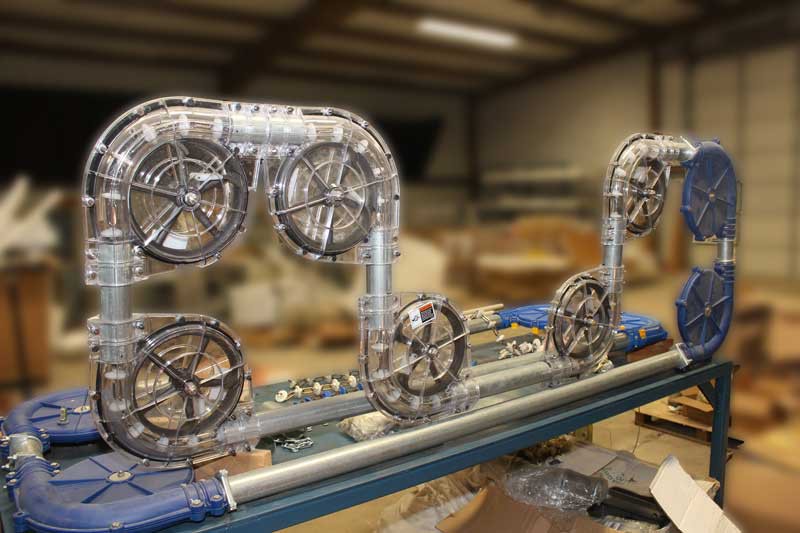
“The drive unit is off of it now,” Tim explained, “but we ran different brands of chain through this setup to show accelerated wear. Look at this…..see the metal filings in the bottom of the corner? Those showed up when we ran the last batch of electroplated chain through the unit. The process of electroplating weakens steel causing it to wear faster.”
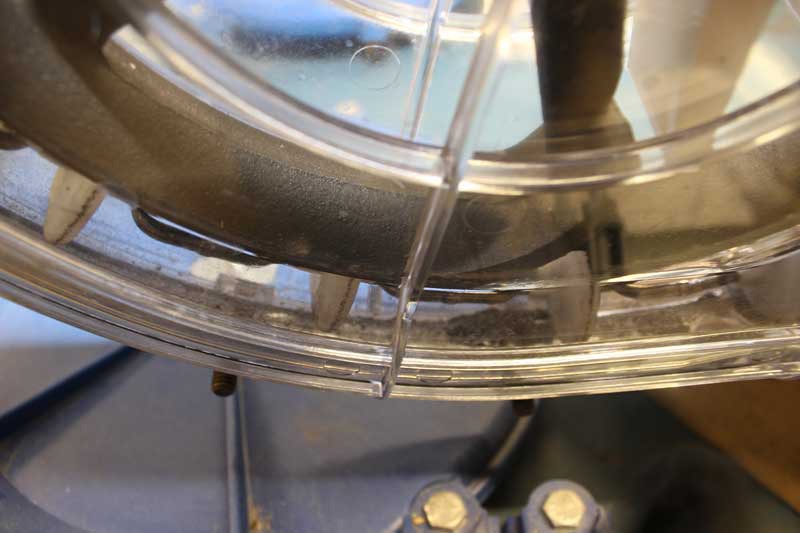
“This confirmed the difference between using hardened steel compared to galvanized or electroplated chain. Hardened steel is high carbon steel given heat treatments of quenching followed by tempering. The result is tough steel chain that resists wear without being brittle. We can run a hardened chain for days and never see filings like that.”
“With most chain feeding systems you have to adjust for “chain stretch” after the systems have operated for awhile. We don’t think the individual chain links stretch but as they go around corners constantly rubbing together they elongate because of wear.”
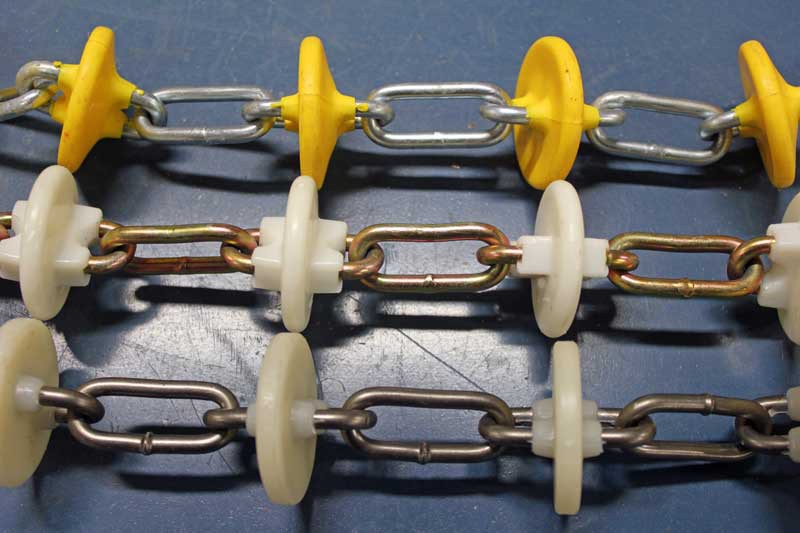
“The only reason, to galvanize steel, is to prevent rust. With the fat and oils in the feed, the chain doesn’t rust in the tube. Most brands of feeding chain is galvanized for it’s appearance before installation. A new bag of Grow-Disk may have some surface rust on it, not a big deal.”
We next looked at how well the plastic disks are fastened to the chain.
“We placed each brand of chain link in a load cell and attached it to a winch, measuring the force needed to pull the disks off the link.”
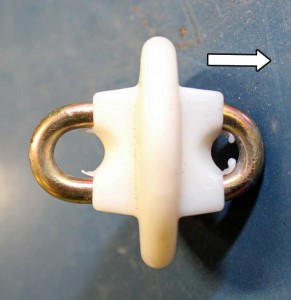
“Most of the disks pulled off at 300 lbs., although one slipped at only 160 pounds! We applied over 600 lbs. of force to the Grow-Disk disk before it slipped.”
“First of all, the disks are manufactured from nylon, a stronger, denser plastic instead of polypropylene.
Second, if you look closely at all the chains the connector welds are smooth, except on the Grow-Disk chain….see the little knob? That knob prevents the nylon disk from slipping…the nylon has to break instead of just slipping.”
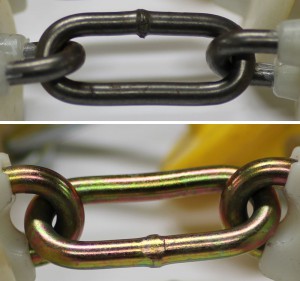
“Most feeding chain suppliers buy general purpose chain with the knob removed. By using a chain fabricated “in-house” and designed specifically for feed systems, we can produce a superior product.”
“A strong plastic disk is important because the drive sprocket powering the entire system makes contact with each, single disk for a brief moment. If an individual disk slips this causes the chain to be slightly out of alignment causing possible jams.”
You can be confident using Grow-Disk chain knowing you are buying the very best even though the cost is usually less.
Hog Slat streamlined distribution system reduces margin stacking. We manufacture and source products direct to you….eliminating extra dealer margins.
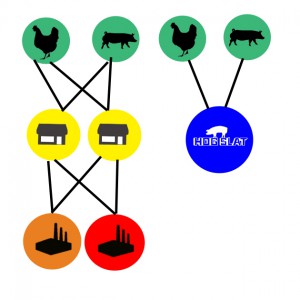
Good product engineering does not add cost to a product but instead takes manufacturing processes into account to reduce costs. It costs no more to spec a hardened chain with knobs intact to provide a better contact for injecting the nylon disk. The result is a superior product that lasts longer on your farm.
Grow-Disk systems, read more…